IndyCar’s all-important hidden development war explained
Although IndyCar is a spec-chassis series, there’s still plenty of areas and parts for teams to develop. Here’s how its tech war plays out
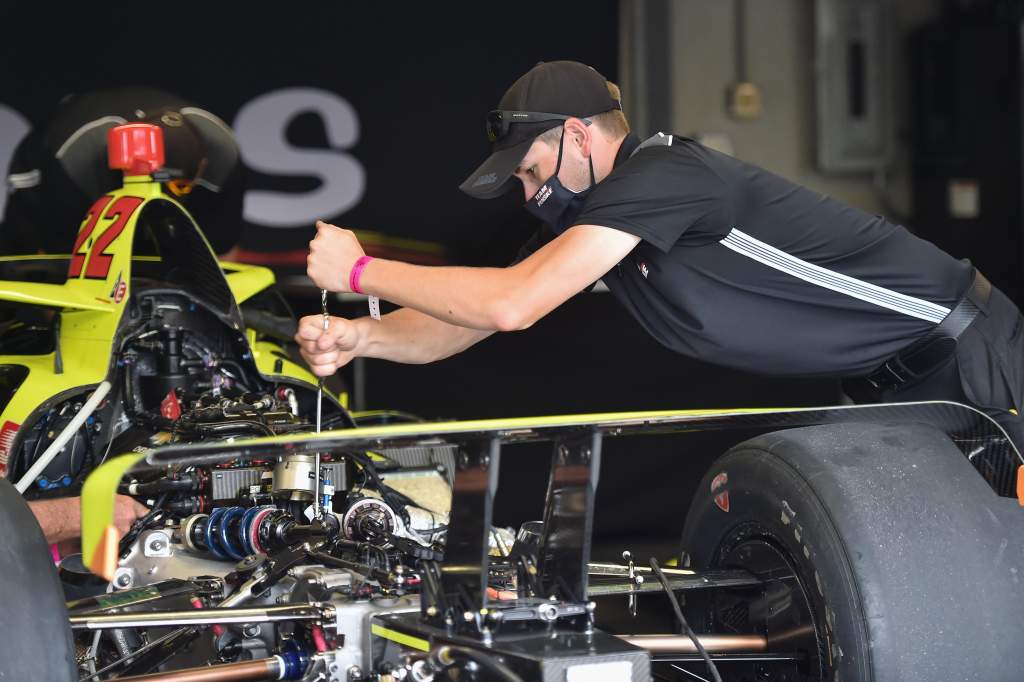
Did you know there’s a very real war going on behind the scenes in IndyCar?
This is supposed to be what many people call a ‘spec series’, but in reality more of the car than you might expect is open for teams to develop.
With the season poised to get under way, The Race has consulted with series insiders and interviewed IndyCar’s vice president of competition and race engineering Bill Pappas to uncover the secrets behind the series’ very real development battle.
What are the key things going on?
The obvious area for teams to develop is the dampers, as they have pretty much free rein over developing those.
There’s also windtunnel testing and putting the car on a shaker rig to simulate the aerodynamic load and the bumps and elevation changes of a track.
The ultimate goal is to keep the car stable under acceleration, braking and cornering to maximise the aero devices on the car, and also to hone a set-up which allows the most of the tyre’s contact patch to touch the ground while not wearing the rubber out too quickly.
It’s then about applying what you’ve learned with your various simulation tools into packages that suit a variety of tracks, with ovals, street courses and road courses making this one of the toughest motorsport nuts to crack.
If you do all of these things well, you’re in the hands of your driver.
Pappas oversees all engineering and technical operations, including chassis and engine development, safety enhancements and aerodynamic initiatives for IndyCar, so he’s the perfect person to shed light on the developments teams are looking for.
He’s also an uber-experienced engineer who won the Indy 500 with Juan Pablo Montoya, so there’s no pulling the wool over his eyes as he’s seen the art of developing cars from the rule makers and rule benders perspective!
Let’s go into some more detail on these development pillars.
Putting a damper on things
Picture courtesy of Matt Fraver/INDYCAR
The role of a damper is relatively straightforward. When the car goes over a kerb or a bump, the springs in the suspension compress. Without a damper turning this energy enacted on the spring into heat, the energy would continue and the car would bounce up and down until the force dissipated.
If the car is bouncing up and down, it’s not creating a level airflow over the car so the aerodynamics aren’t being optimised. Also, the contact patch of the tyre isn’t even, which means the car’s not getting the optimum amount of grip from the tyre, and/or the tyre is wearing in an irregular fashion.
You may have heard teams use the terms ‘bump’ and ‘rebound’. Simply put, the bump is the movement of the wheel upward when riding the elevation change as the springs compress. Rebound is the wheel returning downwards and the spring unloading.
The reason dampers are so important in IndyCar is because the efficiency of the damper package is down to the teams as it’s one of the few areas where they can develop. Most of the other significant parts on the car are to spec. Of course, tyres are the key to the car, like in any other motorsport, as they are what’s in contact with the ground.
“The evolution of where the dampers have gone is to optimise the tyre performance, whether that’s switching the tyre on and getting grip quickly, or keeping the tyre from wearing out,” Pappas tells The Race.
“It’s also platform management. They do all these windtunnel studies and they say, ‘OK, in a 30mph corner, the optimum ride height is this and the rake is that’.
“They spend a lot of time tuning the dampers, we have the use of inerters as well, that’s been something that’s come into play since 2012.
“The teams show up and can do a pretty good job of tuning in their dampers for the conditions, for the track, for the tyres. Teams have really opened up those departments quite a bit to optimise that to that device.”
The inerters Pappas mentions were introduced to motorsport through Cambridge University Enterprise, which licensed the design to McLaren in F1 initially. It’s now better known as the j-damper or mass damper, and the inerter takes suspension energy and dissipates it through a flywheel contained in the device. It’s a third element of the suspension alongside the spring and damper.
Ultimately it helps to regulate the ride height of the car.
Every team in the championship will have at least one person dedicated to dampers with the team supporting them, or even a group especially dedicated to the dampers.
Keeping it breezy
IndyCar teams use full-sized cars in the windtunnel – not models like in F1, although Dallara have used those – and can operate with as many personnel as they like. There’s no limit in the regulations.
Where windtunnel time gets complicated is when, if teams arrange to use a windtunnel, it comes out of their limited number of test days. However, if organised by the engine manufacturers, it doesn’t come out of a team’s allocation.
Therefore Chevrolet and Honda can be running in the windtunnel with as many people as they like, all year around. The fact that they do this and then pass on the data to teams is another reason IndyCar has become closer and more competitive in recent years.
There are only a limited number of facilities that can offer windtunnel testing near to the IndyCar teams, and using full-sized cars. This can make the logistics of arranging windtunnel time difficult. Basically, finances and logistics effectively police windtunnel testing in IndyCar.
The biggest chunk of windtunnel time is dedicated to the series’ blue-ribband event, the Indy 500.
Pappas reckons teams dedicate 60-70% of windtunnel time to working on the event.
“Indianapolis is the crown jewel for everybody,” he says. “It’s the target that everybody’s aiming at.
“They have all the data, they know that if they’re in traffic, the ride-height’s going to do ‘this’, the loads are going to change by ‘this’, how do we optimise that aerodynamically?
“What have we got to do for tilt, for rake, to ensure that the car is in that optimum position when they’re in traffic.
“And then as they get to clean air, then their attitude changes and, how much does that change the downforce?
“They’re looking at all these scenarios to try to say OK, in these conditions you’re going to need to ensure that you have this amount of rake so mechanically you have to set the car up with springs or just static ride height adjustments.
“We also allow ride control devices, third springs front and rear, that control heave (the car moving up or down when gaining or losing downforce).
“So it’s tuning those to ensure that the car is at the optimum platform height to generate the downforce and the drag that they’re looking for racing at the speedway. They spend a lot of time on the 500.”
Different aero packages are also tested in the windtunnel with a variety of different devices available each year, like gurney flaps, wickers or fairings for example, but it’s not only downforce being focused on here.
There’s a somewhat obvious and fundamental aspect to the car itself the teams have to work on.
“Aerodynamic drag usually comes out of fit and finish in the bodywork,” adds Pappas.
“We don’t allow the teams to go off and design and build their own wings or underwing but it’s the fit and finish and there’s quite a bit of difference between teams that run really well year after year and those that don’t.
“The other end of the deal is mechanical drag, and that’s the wheel bearings and all the bearings throughout the car. Trying to minimize any type of stiction.
“Any drag is horsepower loss, so you’re trying to ensure that you don’t lose any of your horsepower.”
This is part of the reason why manufacturers have become more involved in the processes that don’t involve the engine.
The car is a sum of parts and over the last few years Honda and Chevrolet have increased their involvement in the windtunnel to try and optimise the cars both at the 500 and for the rest of the calendar.
Both have significantly developed their simulators too, to the point that all of the teams use their facilities for development work.
More than a mechanic’s lift
Alongside simulation, damper development and windtunnel honing, the shaker rig is a vital tool to IndyCar teams.
It looks a tiny bit like a car lift at your local garage, only much, much more complicated.
“I call that a seven-post rig,” explains Pappas.
“So you put a full-sized car on a platform, and you can simulate aero loading, they have what’s called aero loaders that pull down the chassis.
“You feed in a circuit map, so as the car goes through the corners, the aero comes off so you let the chassis rise up, then will have four pads under each wheel.
“Through simulation, they’ll input the bump pattern of the race track, because we have scanned all our racetracks, and so through that information, again, they’re able to start to fine tune the dampers to optimise ride control for the heave and the pitch like we were just talking a minute ago.”
Think of it like a simulator, but for the car not the driver. The device can simulate the bumps the car will be subjected to on each corner of the track so that the teams can refine the dampers, springs and ride height to get the perfect balance for any given track.
So between the shaker rig and the windtunnel, teams will be aiming to develop ‘packages’ for different types of track, where the car will be set up to react a certain way in fast and slow corners depending on bumps and elevation change.
This helps the teams maximise the tyre contact patch and keep the car level to make the most of the aerodynamics involved.
Like windtunnel testing, there’s very few restrictions on shaker rig testing. Often teams will send their cars back from races straight to the shaker rig for analysis. However, with many outfits chasing time on a limited number of shaker rigs in the Indianapolis are, scheduling and logistics limit the time teams have in these facilities.
What is the key to an IndyCar that handles well?
Fundamentally IndyCar teams – on road and street courses – are trying to set-up the car to remain level and stable through the corners in order to create the optimum and even amount of downforce pushing the car into the ground.
Related to this, the teams are also trying to achieve the optimum contact patch for the tyre – simply put, getting as much of the surface area of the tyre touching the road, but also trading that off against having too much tyre wear and how quickly the tyres can be turned on and in the operating window – or not.
In many other single-seater series which have fewer parts open for development, a team will go through the motions of finding the best settings for the conditions, make a note of them and then they have a base set-up which they can refine. They can only make limited changes, so fundamentally there should be an end goal where that car is optimised for the parts available.
In IndyCar, with so many key parts open for development, changing one small item can cause a set-up chain reaction that totally alters a car’s handling philosophy.
Therefore, with upgrades made, teams are trying to finely balance the car to perform in all conditions.
This is complicated by driving style. The team can create the perfect set-up for each set of conditions on a piece of paper, but if a driver doesn’t like the way the car handles, teams have to find a way to make changes to the car’s performance without totally altering the set-up philosophy they have developed.
As a practical example, this is one of the reasons why Felix Rosenqvist struggled to adapt to the Arrow McLaren SP car this year and why the team couldn’t initiate an immediate fix.
Its car is fastest driven in an aggressive manner – as proven by Pato O’Ward – and initially the team struggled to give Rosenqvist a package more suited to him without compromising its set-up. It tried Rosenqvist’s Ganassi set-ups, but with Arrow McLaren SP’s parts it didn’t have the same effect on the car.
The way the car is finely poised means it’s very difficult for a team or driver to bring one thing their old operation was doing and install it in their new surroundings, because more than likely it will have an affect on the balance.
It’s why Romain Grosjean’s engineer Olivier Boisson told us recently that he was keen to work with Andretti to make sure Grosjean was able to brake as sensationally as he had at Dale Coyne, but that it wasn’t a given there would be successful carry-over.
Hopefully these key areas of development help to explain why slumps can happen for drivers in IndyCar. If the packages the teams have put together don’t work or are too difficult for the driver to get the most out of them, fixing it can be a real issue because of the sum of parts.
It’s very rarely as simple as making a small tweak if your package is well off. And you might have to wait until the off-season when you have the time and facilities to try wholesale changes. You won’t be able to do that mid-season.
It’s another aspect of IndyCar racing which is making the series so fun to watch right now.